This article delves into the causes, effects, and mitigation measures related to flyrock incidents. It emphasises the importance of understanding mechanisms like face bursting, cratering, and rifling, which contribute to flyrock generation. The establishment of clearance zones, determined through predictive models utilizing various approaches, is critical for safeguarding personnel, equipment, and structures. Recent studies indicate a shift towards artificial intelligence techniques, with artificial neural networks and adaptive neuro-fuzzy inference systems gaining prevalence in predicting flyrock trajectories.
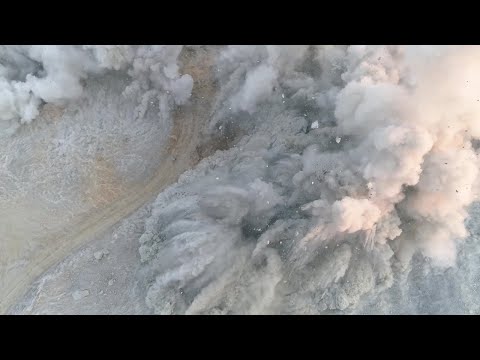
Flyrock’s impact on the safety of personnel, equipment, and structures underscores the imperative need to implement effective mitigation measures. Recent accident statistics emphasize the ongoing hazards, necessitating a proactive approach. Mitigation strategies encompass optimizing blast design, establishing exclusion/clearance zones, complying with relevant laws and regulations, implementing blast monitoring, providing personnel training, and promoting public awareness.
Optimizing blast design is crucial for reducing risks, taking into account factors such as geology and confinement conditions. Utilizing tools like the Scaled Depth of Burial calculation and innovative stemming solutions, such as Varistem Stemming Plugs, contributes significantly to blast optimization. Exclusion zones play a vital role in preventing unauthorized access, and adherence to regulations, such as the Mine Health and Safety Act, ensures strict compliance.
Effective blast monitoring, combined with comprehensive personnel training, enhances safety practices. Real-time systems facilitate prompt corrective actions, while thorough training ensures that personnel are well-versed in safety protocols. Public awareness and communication are indispensable for fostering understanding and cooperation within nearby communities.
Essentially, addressing flyrock risks requires a comprehensive, technology-driven approach, along with strict adherence to regulations and ongoing training and communication initiatives. By implementing these measures, mining and quarrying operations can substantially improve safety and minimize the impact of flyrock incidents.
INTRODUCTION
Blasting activities in mining and quarrying operations play a pivotal role in extracting valuable resources from the Earth’s crust. However, a significant risk associated with blasting is the occurrence of flyrock. Flyrock refers to propelled fragments of rock ejected from the blast site beyond the established clearance zone, posing potential hazards to personnel, equipment, and nearby structures (Esen, 2016). The clearance zone is the designated area around a blast site beyond which the blaster must evacuate all personnel and equipment before initiating the blast (Stiehr, 2011).
Researchers have explored various methods, including artificial intelligence, geotechnics, empirical and statistical approaches, and ballistics, to predict flyrock trajectories and determine the minimum safe clearance zone. This research aims to assist in enhancing blast designs to mitigate flyrock and associated risks. This article seeks to illuminate the phenomenon of flyrock, its causes, effects, and the critical importance of implementing mitigation measures to minimize flyrock risks.
Flyrock occurs when the explosive force of a blast surpasses the confinement capacity provided by the rock mass. This phenomenon can be triggered by several factors, including insufficient blast design, improper loading or stemming, an excessive explosive charge, or unfavorable geotechnical conditions leading to inadequate confinement of the blast energy. The dimensions, speed, and path of flyrock fragments can vary widely, encompassing small particles to sizable boulders that can travel considerable distances from the blast site.
The primary mechanisms of flyrock generation, as illustrated in Figure 1, are categorized into Face Bursting, Cratering, and Rifling.
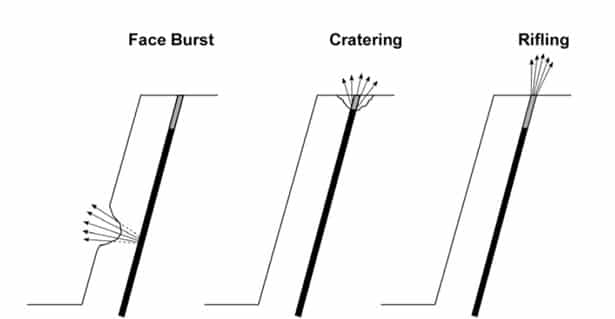
Figure 1: Main Mechanisms of Flyrock Generation (Richards & Moore, 2005)
Face Bursting occurs due to insufficient face burden with the burden conditions usually being the controlling factor for the flyrock distances in front of the face, as shown in the video below
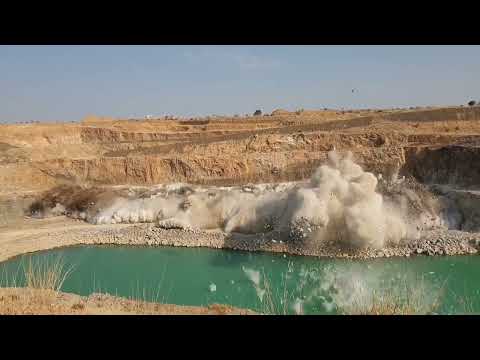
Cratering takes place in the collar of the blasthole and occurs when the stemming height to hole diameter ratio is too small or if the rock in the collar region is of a weaker nature.
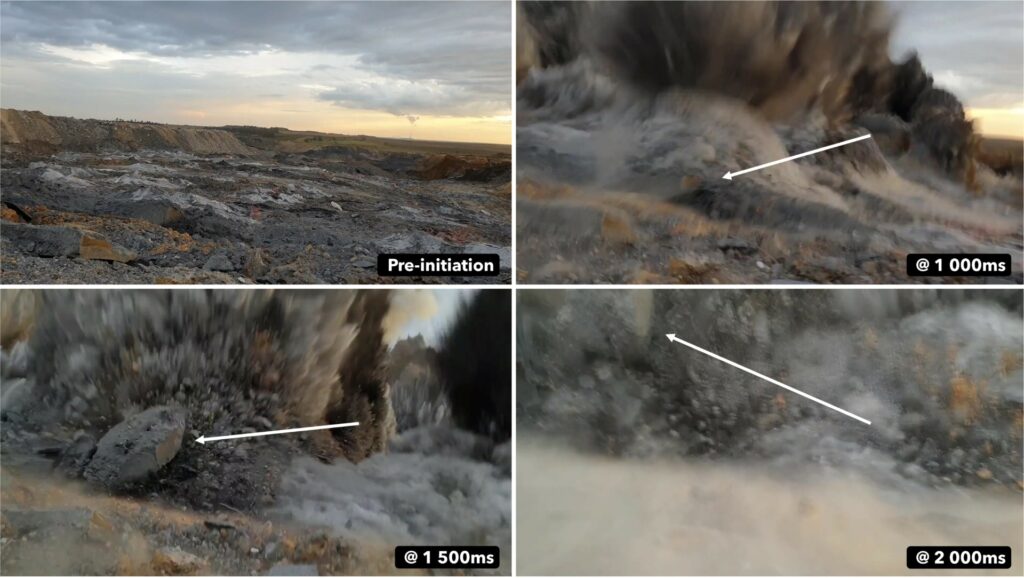
Figure 2: Flyrock Propagation
Rifling, distinct from cratering, occurs in the stemming region and involves the expulsion of stemming material without the formation of a crater. The stemming length is generally sufficient to prevent cratering, but issues may arise if the stemming material lacks the proper characteristics for effective energy confinement or if loose rocks from the collar are ejected along with the stemming material, reaching high trajectories (Richards & Moore, 2005).
Clearance zones typically vary for equipment and personnel, with the personnel clearance often being the more extensive of the two. This distinction is illustrated by the example provided by St. George and Gibson (2001), who utilized Monte Carlo simulations to predict minimum clearance zones, as depicted in Figure 3.
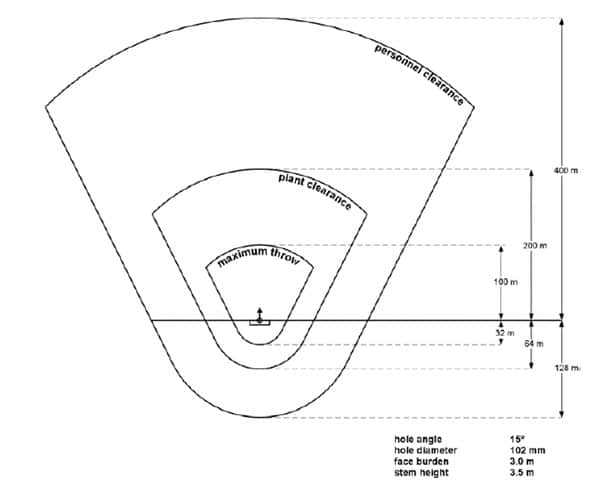
Figure 3: Calculated recommended minimum clearance zone for 102mm blastholes (St George & Gibsin, 2001)
When determining the minimum clearance zone, various predictive formulations and graphs have been developed to assist in predicting flyrock trajectory based on the blast design parameters. An example of this is indicated in Figure 4 which stems from the work done by Lundborg (1981) and indicates the predicted throw distance for various blasthole diameters. This has become the basis of most empirical and statistical flyrock models developed to date.
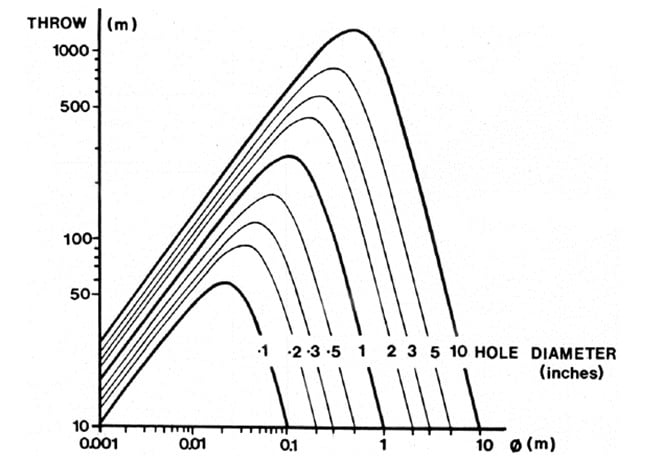
Figure 4: Graph depicting the maximum throw of boulders (Lundborg, 1981)
Van der Walt and Spiteri (2020) conducted an analysis on a range of potential approaches and techniques to predict and investigate flyrock as found in publications dating from 2010 to 2020. The authors concluded that although the actual impact of blast design on the risk of flyrock is still debated, these proposed solutions were site-specific and not directly transferrable to different sites. It was further stated that a more objective, accurate and quantitative method of measuring the travel distance of flyrock is required. Table 1 indicates a summary of the proposed flyrock models found in literature.
Table 1: Proposed Flyrock Models since 2010 as found in literature (after Van der Walt and Spiteri, 2020)
Type of approach | Description | References |
Artificial Intelligence (AI) | The use of Artificial Neural Networks (ANNs) and Adaptive neuro-fuzzy inference systems (ANFISs) to model and interpret real-world scenarios | (Monjezi, et al., 2010) (Monjezi, 2012) (Raina, et al., 2013) (Ghasemi, et al., 2014) (Marto, et al., 2014) (Kukreja, et al., 2016) (Trivedi, et al., 2015) (Armaghani, et al., 2016a) (Raina & Murthy, 2016) |
Rock Engineering Systems (RES) | Used to evaluate the interaction and influence of relevant parameters to reduce uncertainty and to determine the influence of parameters on the overall system. | (Faramarzi, et al., 2014) |
Empirical and statistical analysis | Foundation of most predictive approaches since the 1980’s. This approach aims to predict the maximum throw resulting from a blast based on observations and historical data. Due to the vast number of variables, this approach have not been favoured in most of the recent studies | (Ghasemi, et al., 2012) (Armaghani, et al., 2016b) (Dehghani & Shafaghi, 2017) (Hasanipanah, et al., 2017) |
Forensic or Ballistics approach | This approach relies on globally accepted first principles of physics and natural laws with flyrock assumed to follow the principles of projectile motion. This is used to determine the trajectory and distance of flyrock particles based on shape, size, velocity and the law of conservation of energy. | (Stojadinovic´, et al., 2011) (Stojadinovic´, et al., 2013) (Stojadinovic´, et al., 2015) |
A summary graph depicting the distribution of flyrock prediction techniques can be seen in Figure 5. From this it is evident that the majority of recent studies relating to flyrock prediction models (53%) rely on AI techniques (ANN and ANFIS).
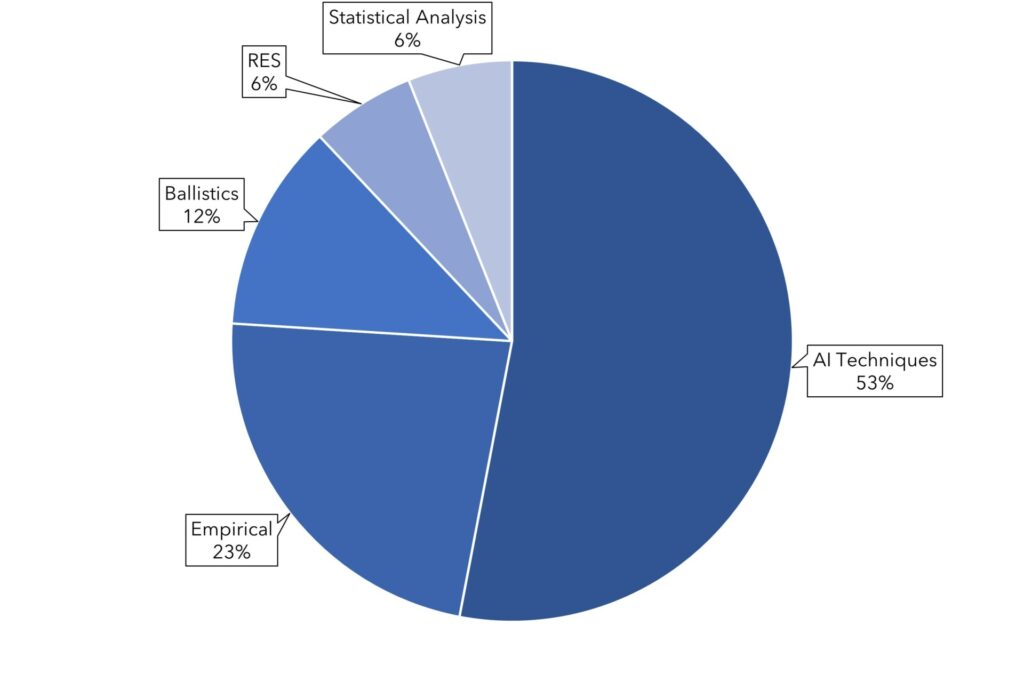
Figure 5: Distribution of flyrock prediction techniques in recent studies (Van der Walt & Spiteri, 2020)
EFFECTS OF FLYROCK
Equipment Damage
Flyrock can cause damage to machinery, vehicles, and equipment present near the blast site. The impact of these projectiles can result in significant downtime, repair costs, and potential delays in mining or quarrying operations.
Structural Damage
If flyrock reaches nearby structures, such as buildings, infrastructure, or utilities, it can cause substantial damage, including structural weakening, shattered windows, or even the collapse of vulnerable structures.
Personnel Safety
Flyrock can pose a significant risk towards the health and safety of employees or persons within the vicinity of the mine (Van der Walt, 2019). The high velocity and unpredictable trajectory of flyrock fragments can cause serious injuries or fatalities if individuals are struck by them. According to multiple authors (Table 2) flyrock accidents still make up a high percentage of blasting induced accidents. Therefore, mitigating the risk of flyrock is critical towards achieving safer blasting operations.
Table 2: Recent references of flyrock related accidents (Raina, et al., 2015)
Reference | Period | Blasting Injuries | % of Flyrock Injuries in blasting related accidents |
Bajpayee et al. (2004) | 1978-1998 | 281 | 41% |
Little (2007) | 1978-1998 | 412 | 68% |
Kecojevic and Radomsky (2005) | 1978-2001 | 195 | 28% |
Verakis and Lobb (2007) | 1994-2005 | 168 | 19% |
Mishra and Mallick (2013) | 1996-2004 | 30 | 24% |
Verakis (2011) | 2010-2011 | 18 | 38% |
Ashikari (1999) | – | – | 20% |
MITIGATION MEASURES
To mitigate the risks associated with flyrock in blasting activities, several crucial measures can be implemented. These include optimizing blast design, establishing clearance zones, complying with regulations, monitoring and controlling blasts, providing personnel training, raising public awareness, and enhancing overall communication.
Blast Design Optimisation
Effective blast design is pivotal in mitigating flyrock hazards. Engineers can significantly reduce the likelihood of flyrock occurrences by carefully considering factors such as geology, rock properties, and confinement conditions. Optimization of blast parameters, including explosive type, charge weight, timing, and stemming, is essential. Through the utilization of RES techniques and historical data, engineers can analyze the influence of these parameters on the overall blast outcome, enabling them to refine and optimize the design.
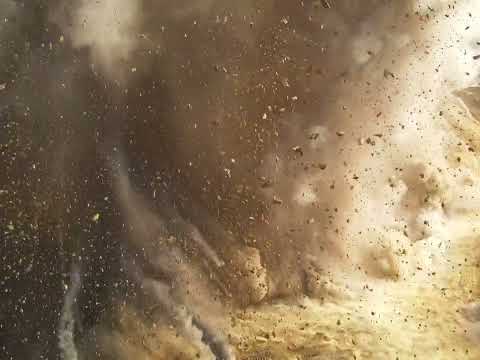
A critical parameter related to energy containment is stemming. During blasting activities, it is imperative for the blaster to ensure the correct stemming material and stemming length are employed. The Scaled Depth of Burial (SD) calculation (Figure 6) serves as a valuable tool in determining adequate confinement.

Figure 6: Schematic depicting the Scaled Depth of Burial Principle (BAI, 2008)
SD is an empirical measure of blast energy confinement, representing the ratio of the stemming material to the amount of explosive within a space equivalent to 10 hole diameters (Tobin, 2013). The schematic illustrates SD, depicting how the ratio of stemming to explosives influences blast energy containment. Higher SD values indicate deeper burial depths, potentially leading to increased controlled energy and reduced surface activity. By considering the scaled depth of burial in blasting design and execution, it becomes possible to mitigate potential environmental impacts associated with ground vibrations, air overpressure, and flyrock.
An example of an engineering tool/device contributing to flyrock mitigation through blast optimization is the Varistem Stemming Plug. Deployed in mining, quarrying, and civil blasting applications, these plugs offer various advantages owing to their capacity to sustain energy within a blasthole for an extended duration. The benefits encompass enhanced and more uniform fragmentation, a decrease in flyrock occurrences, improved noise and airblast profiles, and concurrently, productivity gains and cost savings in subsequent processes.
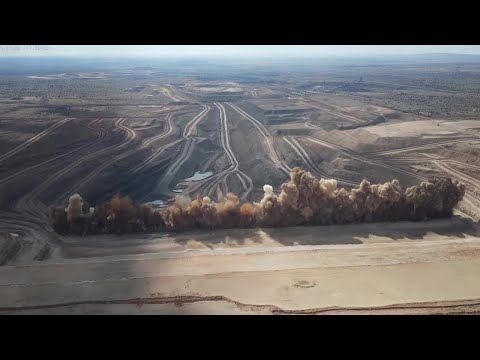
VIDEO: Varistem Energy Retention Comparison
Exclusion/Clearance Zones
Establishing exclusion/clearance zones around the blast site helps prevent unauthorised personnel from entering potentially hazardous areas. These zones should be clearly marked and communicated to all personnel to ensure their safety. The mine should conduct a thorough risk assessment and use tools such as max flyrock throw prediction models to assist in determining the best suited clearance distance.
Adhering to Appropriate Laws and Regulations
The mine and its blasting team should ensure that all blasting activities adhere to the standards and regulations set out by governing bodies and the accompanying legislation. It is also critical that the mine and its employees stay abreast of any amendments to these regulations. For example, the Department of Mineral Resources and Energy (DMRE) is responsible for the oversight of the mining industry in South Africa. In a South African legislative context, explosives are governed by the Occupational Health and Safety Act (OHSA) No. 85 of 1993, the Explosives Act No. 15 of 2003 and Chapter 4 of the Mine Health and Safety Act (MHSA) of 1996 (Els, 2021). The MHSA, 1996 (Act No. 29 of 1996) specifically states the following with regards to blasting activities and flyrock (or fly material) mitigation:
Precautionary measures before initiating explosive charges
4.7 The employer at any mine must take reasonable measures to ensure that when blasting takes place, air and ground vibrations, shock waves and fly material are limited to such an extent and at such a distance from any building, public thoroughfare, railway, power line or any place where persons congregate to ensure that there is no significant risk to the health or safety of persons.
Shot holes to be stemmed and tamped
4.14 The employer at any mine must take reasonable measures to ensure that:
(1) no explosives contained in a shot hole are initiated unless a portion of the shot hole between the explosive charge and the collar of the shot hole is stemmed and tamped by means of a material determined for that purpose by the employer in consultation with the explosives manufacturer or supplier and stemming manufacturer or supplier, to prevent persons from being exposed from the significant risks associated with explosives detonating outside the shot hole, blow outs, fly rocks and harmful explosives gases escaping from the shot hole.
(2) the length of stemming and tamping of a portion of a shot hole between the explosive charge and the collar of a shot hole is determined by means of a risk assessment conducted by the employer in consultation with the explosives manufacturer or supplier, stemming manufacturer or supplier and the competent person contemplated in regulation 14.1 (8). The risk assessment must consider at least the following:
(a) coupling ratio of explosives;
(b) energy released to protect in situ rock;
(c) containment of fly rock and air blast;
(d) blast design and type of explosives;
(e) geology and type of rock; and
(f) safety in dealing with misfired holes.
(3) the material used for stemming and tamping complies with SANS 120:2009, Edition 2 “Stemming for use in blasting”;
Amount or mass of explosives in a shot hole
4.15 The employer at any mine must take reasonably practicable measures to ensure that the maximum amount or mass of explosives used per shot hole is according to the manufacturer’s or supplier’s recommendations.
General precautions
4.16 The employer must take reasonable measures to ensure that:
(1) at any mine other than a coal mine, no explosive charges are initiated during the shift unless-
(a) such explosive charges are necessary for the purpose of secondary blasting or reinitiating the misfired holes in development faces;
(b) written approval for such initiation has been granted by a person authorised to do so by the employer; and
(c) reasonable precautions have been taken to prevent, as far as possible, any person from being exposed to smoke, fumes or fly rocks from such initiation of explosive charges;
(2) no blasting operations are carried out within a horizontal distance of 500 meters of any public building, public thoroughfare, railway line, power line, any place where people congregate or any other structure, which it may be necessary to protect in order to prevent any significant risk, unless:
(a) a risk assessment has identified a lesser safe distance and any restrictions and conditions to be complied with;
(b) a written application is submitted to the Principal Inspector of Mines accompanied by the following documents for approval-
(i). a sketch plan indicating the distance from the blasting area to the affected structures;
(ii). the risk assessment;
(iii). a proof of consultation with the owners of the affected structures; and
(iv). restrictions and conditions.
(c) a written approval has been granted by the Principal Inspector of Mines; and
(d) any restrictions and conditions determined by the Principal Inspector of Mines are complied with. (MHSA, 1996)
Blast Monitoring and Control
Implementing real-time blast monitoring systems, including high-speed cameras, acoustic sensors, and seismographs, allows for immediate feedback and control over blasting operations. Monitoring helps detect any deviations from the intended blast design, enabling prompt corrective actions to prevent flyrock incidents.
Blast Personnel Training
Providing comprehensive training to blasting personnel is crucial in ensuring safe and responsible blasting practices. This includes educating them on proper blast design, loading techniques, stemming procedures, standards and regulations, and the use of protective measures to minimise the risks of flyrock.
Public Awareness and Communication
Maintaining open communication channels with nearby communities and stakeholders is essential in raising awareness about the potential hazards of flyrock. Regular communication, sharing of blast schedules, and addressing concerns help foster understanding and cooperation.
CONCLUSIONS
In conclusion, the extraction of valuable resources from the Earth’s crust through blasting activities in mining and quarrying operations is vital, but it comes with significant risks, particularly the occurrence of flyrock. Flyrock, propelled rock fragments that exceed the determined clearance zone, poses serious threats to personnel, equipment, and nearby structures. This article has provided an in-depth exploration of flyrock, covering its causes, effects, and the importance of implementing mitigation measures to minimize risks.
Understanding the mechanisms of flyrock generation, such as face bursting, cratering, and rifling, is crucial for developing effective predictive models. The establishment of clearance zones, calculated based on various predictive formulations and graphs, plays a pivotal role in ensuring the safety of personnel and equipment. Recent studies have explored different approaches, with artificial intelligence techniques, specifically artificial neural networks (ANNs) and adaptive neuro-fuzzy inference systems (ANFIS), gaining prominence in predicting flyrock trajectories.
The effects of flyrock on personnel safety, equipment damage, and structural integrity underscore the necessity of implementing mitigation measures. Recent accidents statistics highlight the persistent danger of flyrock, emphasizing the urgency of addressing this issue. Mitigation measures include blast design optimisation, exclusion/clearance zones, adherence to laws and regulations, blast monitoring and control, personnel training, and public awareness and communication.
Blast design optimisation, considering factors like geology, rock properties, and confinement conditions, is crucial in mitigating flyrock hazards. Tools such as the Scaled Depth of Burial calculation and engineering innovations like the Varistem® Stemming Plug contribute to blast optimisation.
Exclusion/clearance zones help prevent unauthorized entry into hazardous areas, and adherence to laws and regulations, such as those outlined by the Mine Health and Safety Act, is imperative.
Blast monitoring and control, coupled with personnel training, contribute to safe blasting practices. Real-time monitoring systems enable immediate corrective actions, while comprehensive training ensures that blasting personnel are well-versed in safety protocols. Public awareness and communication are essential for fostering understanding and cooperation within nearby communities.
In summary, the mitigation of flyrock risks requires a multi-faceted approach involving technological advancements, adherence to regulations, and a commitment to ongoing training and communication. By implementing these measures, mining and quarrying operations can significantly enhance safety and reduce the impact of flyrock incidents on personnel, equipment, and surrounding structures.
REFERENCES
Armaghani, D., Mahdiyar, A., Hasanipanah, M. & Faradonbeh, R., 2016b. Risk assessment and prediction of flyrock distance by combined multiple regression analysis and Monte Carlo simulation of quarry blasting. Rock Mechanics and Rock Engineering, 49(9), pp. 3631-3641.
Armaghani, D., Tonnizam, E., Hajihassani, M. & Abad, S., 2016a. Evaluation and prediction of flyrock resulting from blasting operation using empirical and computational methods. Engineering with Computers, 32(1), pp. 109-121.
BAI, 2008. Resources/ Scaled depth of Burial Diagram. [Online]
Available at: chrome-extension://efaidnbmnnnibpcajpcglclefindmkaj/https://ergindustrial.com/wp-content/uploads/2022/08/Scaled-Depth-of-Burial.pdf
[Accessed 14 November 2023].
Bajpayee, T. et al., 2003. Fatal accidents due to flyrock and lack of blast area security and working practices in mining. Journal of Mines, Metals and Fuels, 51(11/12), pp. 344-350.
Dehghani, H. & Shafaghi, M., 2017. Prediction of blast-induced flyrock using differential evolution algorithm. Engineering with Computers, 33(1), pp. 149-158.
Els, R., 2021. Investigation into the effectiveness of blast stemming devices for surface blasting, University of Pretoria: s.n.
Esen, S., 2016. Effective fragmentation and flyrock control stratigies at quarries. s.l., s.n.
Faramarzi, F., Mansouri, H. & Farsangi, M., 2014. Development of rock engineering systems-based models for flyrock risk analysis and prediction of flyrock distance in surface blasting. Rock Mechanics and Rock Engineering, 47(4), pp. 1291-1306.
Ghasemi, E., Amini, H., Atae i, M. & Khalokakaei, R., 2014. Application of artificial intelligence techniques for predicting the flyrock distance caused by blasting operation. Arabian Journal of Geosciences, 7(1), pp. 193-202.
Ghasemi, E., Sari, M. & Ataei, M., 2012. Development of an empirical model for predicting the effects of controllable blasting parameters on flyrock distance in surface mines. International Journal of Rock Mechanics and Mining Sciences, Volume 52, pp. 163-170.
Hasanipanah, M., Faradonbeh, R., Armaghani, D. & Amnieh, H., 2017. Development of a precise model for prediction of blast-induced flyrock using regression tree technique. Environmental Earth Sciences, Volume 76, p. 27 (10).
Kukreja, H., Bharat h, N., Siddesh, C. & Kuldeep, S., 2016. An introduction to artificial neural network. International Journal of Advance Research and Innovative Ideas in Education, 1(5), pp. 27-30.
Lundborg, N., 1981. The probability of flyrock damage. Report DS 1981:5, Stockholm, Sweden: Swedish Detonic Foundation (SveDeFo).
Marto, A. et al., 2014. A novel approach for blast-induced flyrock prediction based on imperialist competitive algorithm and artificial neural network. The Scientific World Journal, 5(doi: 10.1155/2014/643715).
MHSA, 1996. Mine Health and Safety Act 29 of 1996 and Reguations. Capte Town: Republic of South Africa, Government Gazette.
Monjezi, M., Amini Khoshalan, H. & Yazdian Varjani, A., 2010. Prediction of flyrock and backbreak in open pit blasting operation: a neuro-genetic approach. Arabian Journal of Geosciences, 5(3), pp. 441-448.
Monjezi, M. M. A. M. A. a. K. M., 2012. Evaluation of effect of blast design parameters on flyrock using artificial neural networks. Neural Computing and Applications, 23(2), pp. 349-356.
Raina, A. & Murthy, V., 2016. Importance and sensitivity of variables defining throw and flyrock in surface blasting by artificial neural network method. Current Science, 111(9), pp. 1524-1531.
Raina, A., Murthy, V. & and Soni, A., 2013. Relevance of shape of fragments on flyrock travel distance: An insight from concrete model experiments using ANN. Electronic Journal of Geotechnical Engineering, Volume 18, pp. 899-907.
Raina, A., Murthy, V. & Soni, A., 2015. Flyrock in surface mine blasting: Understanding the basics to develop a predictive regime. Current Science, 108(4), pp. 660-665.
Ranathunga, R. et al., 2019. Flyrock Generation and Social Impact Mitigation in Local Quarrying. s.l., s.n., pp. 33-38.
Richards, A. & Moore, A., 2005. Kalgoorlie Consolodated Gold Mines: Golden Pike cut-back flyrock control and calibration of a predictive model, s.l.: TERROCK Consulting Engineers.
St George, J. & Gibsin, M., 2001. Estimation of flyrock travel distances: A probabilistic approach, Hunter Valley, New South Wales, Australia: Explo.
Stiehr, J., 2011. Flyrock. In: J. Stiehr & J. Dean, eds. ISEE Blasters’ Handbook. 18th ed. Cleveland(Ohio): International Society of Explosives Engineers, pp. 383-410.
Stojadinovic´, S. et al., 2015. Prediction of flyrock launch velocity using artificial neural networks. Neural Computing and Applications, 27(2), pp. 515-524.
Stojadinovic´, S., Lilic, N., Pantovic´, R. & Žikic´, M., 2013. A new model for determining flyrock drag coefficient. International Journal of Rock Mechanics and Mining Sciences, Volume 62, pp. 68-73.
Stojadinovic´, S., Pantovic´, R. & Žikic´, M., 2011. Prediction of flyrock trajectories for forensic applications using ballistic flight equations. International Journal of Rock Mechanics and Mining Sciences, 48(7), pp. 1086-1094.
Tobin, G., 2013. The Importance of Energy Confinement to the Blast Outcome & Justification for use of Stemming Plugs in Over Burden Removal, Australia: ORSOME Products.
Trivedi, R., Singh, T. & Gupta, N., 2015. Prediction of blast-induced flyrock in opencast mines using ANN and ANFIS. Geotechnical and Geological Engineering, Volume 33, pp. 875-891.
Van der Walt, J., 2019. Developing a concept that can be used to quantify the motion of flyrock, with the intention of eventually producing a measuring tool for future flyrock research, s.l.: Department of Mining Engineering of the University of Pretoria.
Van der Walt, J. & Spiteri, W., 2020. A critical analysis of recent research into the prediction of flyrock and related issues resulting from surface blasting activities. The Journal of the Southern African Institute of Mining and Metallurgy, 120(12), pp. 701-714.