In our business, we are in a unique position where we get to spend time at countless sites, working with drillers and blasters during the planning, preparation, and execution of blasts. Our time spent on sites is mostly on blast day, where the pressure is on to charge, stem, tie-up and set off the blast.
Across many sites, we have observed several impactful good practices relating to blast execution. The list is not meant to be exhaustive, but rather a representation of the most prominent good practices that we have learnt.
Quality Assurance and Quality Control
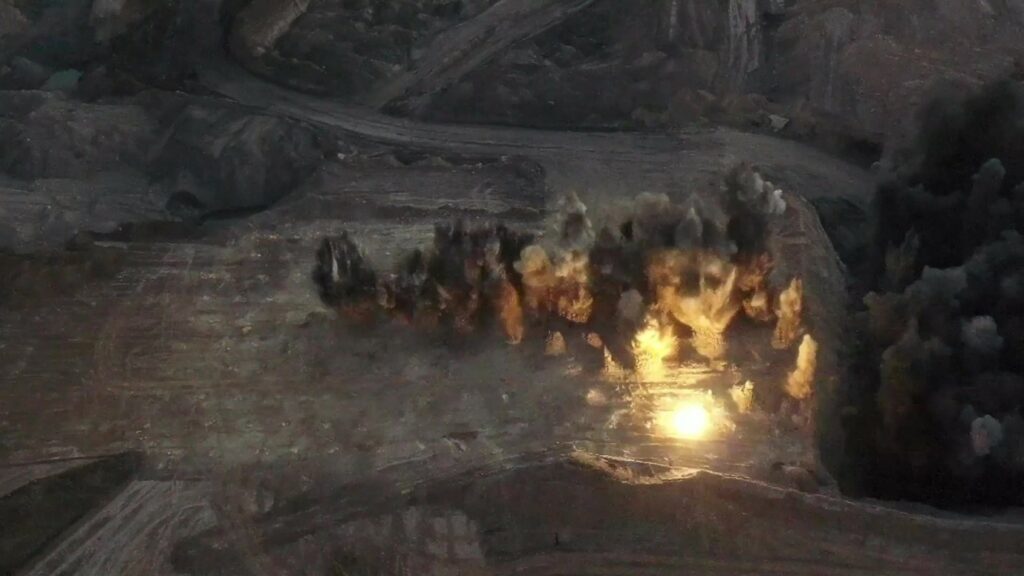
Charging: Although overcharged holes look spectacular in footage, they have an adverse impact on fragmentation and greatly increases the probability of flyrock. Fixing overcharged holes can be a tedious and laborious task, and often times we have seen that the right tool for the job is not available on site. Having a tool available that can safely remove explosives from blastholes is very valuable. In many cases the explosives provider has such a tool, but we would recommend that a spare “in-house” one be available as a Plan B.
The extra effort put into fixing overcharged holes will be rewarded in the blast result that you achieve. In the ideal world, each hole would be charged exactly as per the design. In reality, quality assurance (e.g. explosives removal tool) and quality control (e.g. stemming checks) measures should be in place to get as close to the design as possible.
Stemming:
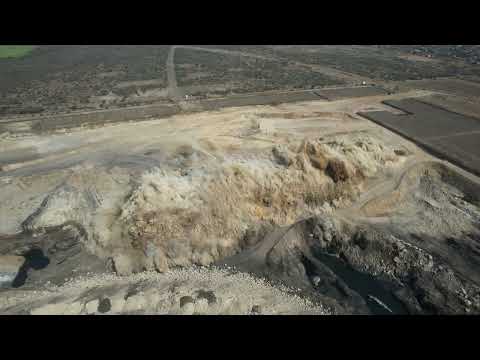
We always say that energy is lazy – it will take the path of least resistance. And in the case of blasting, this is mostly up and out of the blastholes. But not if your stemming practices are up to standard.
Good stemming practices is probably one of the most underrated activities in blasting. There is immense value in “doing stemming right”. The more robust the stopping power in your holes, the more the energy that will be utilized towards breaking your rock mass.
In the vast majority of cases, aggregate beats drill chippings every day. Using aggregate is not always possible due to costs/availability, especially on the more remote mining sites. Drill chippings are the second choice, and depending on the characteristics and size of the chippings, the effectiveness can pale in comparison to aggregate.
Create that stopping power with appropriate stemming, even if it costs more. Look into some additional help from engineered stemming devices like Varistem stemming plugs. You will thank yourself later when you see the difference in blast outcomes.
Blasthole Protection
Drilling of blastholes is an expensive activity, and blastholes should be protected once they have been drilled. Mining is a rough environment, and there are a lot of things that can happen to a blasthole before being charged that can have a negative impact (both in terms of cost and blast performance).
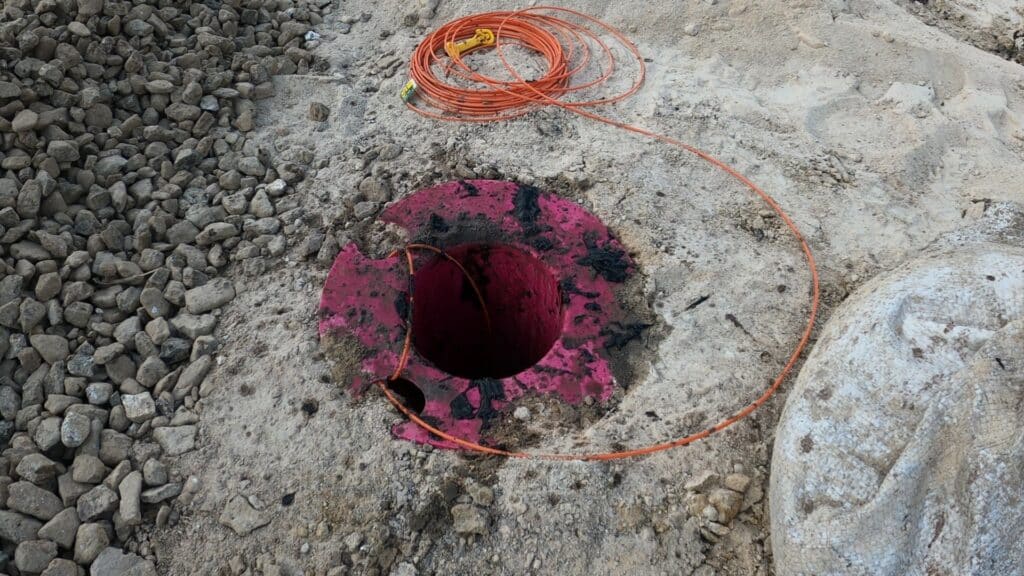
Re-drills is a swear word in mining. A lot of re-drills are simply due to unfortunate geology and rock characteristics. Others are mostly avoidable by ensuring that blastholes are properly protected by using devices like Pink Collar Protection Cones or Blasthole Covers.
Apart from re-drills, not protecting your holes from potential debris falling in can lead to a blocked hole, causing a range of other problems. And possibly another re-drill or short hole if you can’t fix the problem.
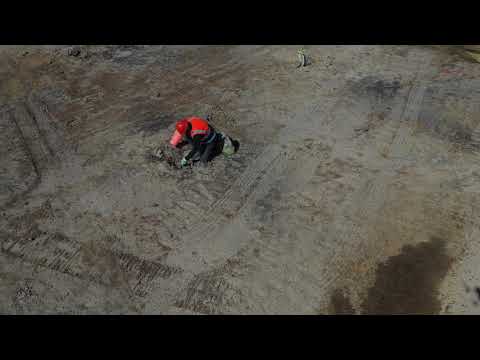
A final point on protecting blastholes – they need to be protected after charging and before stemming as well (a product like the Pink Collar Protection Cones were designed specifically for this purpose). Our experience on sites is that the most amount of debris gets into holes during this window period. We have personally spent hours trying to dislodge rocks that fell into holes after charging, with limited success. The consequence of this is then a hole that can not be properly stemmed and loses large amounts of energy, and in certain cases a great increase in the risk of flyrock.
Dynamic Blast Design
At each new site that we spend some time at, we always ask about the blast design. Based on the results that we have seen, a dynamic approach to blast design seems to yield the best results. Each blasting block/area is unique, and should be treated as such. Factors like block geometry, geology, rock characteristics and on-site conditions should be taken into account when designing blasts.
Preventative Maintenance on Drill Rigs and MMU’s
Machines in mining break frequently, and that is a reality. Conditions are tough. We have the power to reduce the number of unexpected breakdowns by doing preventative maintenance. It is Murphy’s law that a critical piece of equipment will break when needed most on a blast block. I have seen this many times, and this is something that can actively be mitigated through diligent preventative maintenance.
Drone Footage for Blast Analysis
Blasts happen very quickly. Too quick for our eyes to really understand what is going on. On a biological level, our eyes are just not capable of capturing super fast visual changes accurately. What happens is that we see only fragments of the truth, and our brains fill in the blanks.
The human eye can see between 30 – 60 frames per second. An entry-level drone can see at 240 frames per second at a resolution of 1080p.
For each blast that we participate in, we always have a drone (or two drones), filming at 240 frames per second. This basically gives us visibility on every 4 milliseconds of the blast. For post-blast analysis, this is absolute gold.
Even if you are filming your blasts with a standard camera or a cellphone camera, seriously consider investing in an entry-level drone to film your blast. The learnings from this will quickly pay back your investment. We often see things that would have never been possible with the naked eye or with a standard camera.
And finally – You want art, respect the artist!
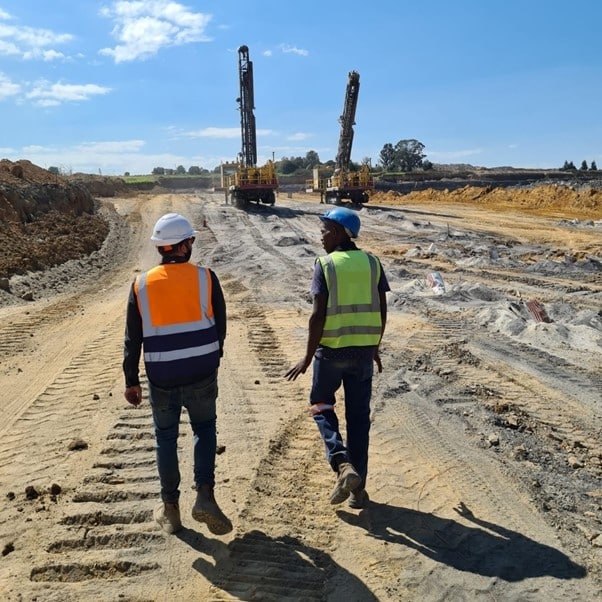
Quality almost always beats quantity with blasting. In the mining world there are always production pressures and tight schedules. The one area that should not be rushed is drilling and blasting. The activities should be both effective and efficient, and this is not always possible when time is constrained.
Ever heard the saying “you can’t rush a good thing”?
Good blasting is art, and blasters are the artists. We expect excellent results every time from blasters, but we almost never provide them with the environment to be both effective and efficient. Want art? Give the artist their tools and their time, and you will get it.