Introduction
Pre-split blasting is a vital controlled blasting technique used in surface mining, quarrying and construction operations to preserve the stability of final pit walls, roadway cuts and retaining walls. It is primarily employed in the mining and quarrying industries to prevent blast-induced damage, minimize overbreak, and maintain long-term slope integrity. As pit depths increase and geotechnical risks mount, the importance of accurate and effective pre-splitting grows. Pre-splitting is not only a technical requirement but also a strategic tool to achieve better safety, economic efficiency, and design conformance in open pit and quarry operations. This specialist technique is, however, not a one size fits all solution and may not be a practical or feasible practice for some operations due to the influence of geological conditions, available equipment, available expertise, and cost constraints. Applicability and the implementation methodology followed will, therefore, vary according to site specific conditions.
Pre-Split Blasting Basics
Pre-split blasting, or ‘pre-shearing’, involves drilling a row of closely spaced, lightly charged holes along the final excavation limits. These holes are fired before the main production blast to create a tensile fracture plane that halts the propagation of blast energy beyond the designed excavation boundary (see Figure 1).
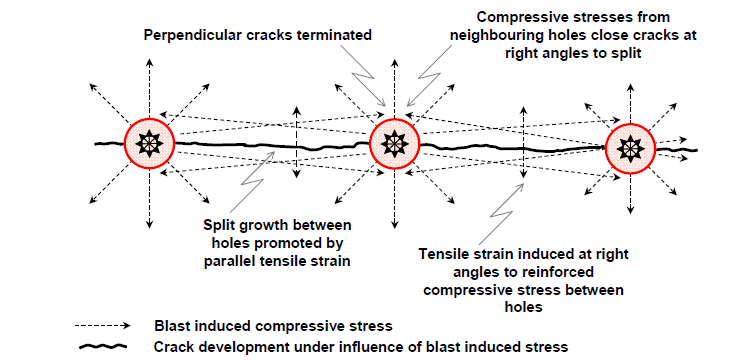
Figure 1. Schematic depicting crack growth mechanism of a pre-split (Tose, 2006)
The resulting split surface protects the highwall from overbreak and structural damage, contributing to safer and more stable benches. Effective pre-splitting depends on several technical parameters, including but not limited to; hole diameter, hole spacing, splitting factor, charge configuration, timing design and geological conditions. Accurate drilling (within ±150 mm), appropriate inclination angles (20° – 30° off vertical), and alignment to avoid major joints are also critical for effective results. Pre-split blasting is not only used in mining and quarrying but also plays a significant role in civil and construction projects. In these industries, pre-splitting is commonly used in the construction of highways, tunnels, dams, and slope stabilization projects. The objective is to produce clean and stable cut slopes that minimize long-term maintenance and reduce the risk of rockfalls. In civil works, hole spacing is often tighter (e.g., 50 mm –75 mm in diameter, spaced 200 mm – 400 mm apart) to accommodate shallower depths and stricter tolerances. Drill accuracy, charge decoupling, and strict timing control are essential to success. Pre-split results in such applications often determine the safety and cost-effectiveness of subsequent construction activities (see Tose, 2006; Chiappetta, 2014; Konya, 2019, Sanders and Tims, 2025). Establishing an appropriate presplit design, whether it be for the first design to be blasted at a site or auditing current practices at a site, starts with identifying the applicable industry standards for pre-split blasting.
At the IQPC Drill and Blast Africa conference held in Johannesburg South Africa, Chiappetta (2014) shared twelve rules for presplitting and highwall control which he believed would yield guaranteed results. The guidelines were for medium to large diameter holes (127mm- 311mm) and are as follows:
- Cp of rock (compressive strength, commonly known as UCS) must be at least 40 MPa.
- Need good drilling controls.
- Powder Factor (PF) should be between 0.40 and 1.0 Kg/m2 (0.08 and 0.20 lbs/ft2) for 10m – 50 m hole depths.
- Wet holes: Reduce powder factor by 25 to 50%.
- Always fire presplit line in advance, before any other holes are drilled on block.
- Fire presplit holes instantaneously.
- Drill presplit holes with 0.50 – 1.0 m subgrade – Below targeted floor or coal seam.
- Buffer hole offset = 10 x buffer hole diameter.
- Use full column explosives in all buffer holes. No air decks or explosive decks.
- If crest overhang: Use a mid-column and bottom hole charge, fired instantaneously.
- Protect presplit charges from contamination and dilution.
- Assure presplit plane does not undercut major joint systems.
At the International Symposium on Stability of Rock Slopes in Open Pit Mining and Civil Engineering held in Cape Town South Africa, Tose (2006) presented his paper on pre-split blasting titled: “A review of the design criteria and practical aspects of developing a successful pre-split”. The author presented a methodology used by AECI mining (AEL at the time) to create a pre-split design that delivers stable highwalls for the life of a mining operation. Although the paper focuses on various perimeter blasting techniques, this article only focused on the content relevant to the topic of pre-split blasting. According to Tose (2006) the following design rules of thumb are relevant for appropriate pre-split designs:
- Maximum depth 15-25m (limited by drilling accuracy).
- Must be fired simultaneously (where possible).
- Typical spacing: 8-16 hole diameters.
- Presplitting should be avoided where the burden to the free face is less than 180 hole diameters.
- Strong rock can be blasted with wider patterns and increased explosives charges.
- Weak rock requires the minimum economic spacing of holes, with limited charges.
- Split factor for surface pre-splitting: 0.30-0.60 kg/m2
- Split factor for dimensional stone: 0.15-0.30 kg/m2
- Where ground vibrations are likely to disturb residents, 17ms HTDs or 12ms Dogbone relays should be inserted into the trunkline at intervals so as to obtain the consecutive firing of smaller groups of blastholes.
- Where noise is to be minimised, surface lines of detonating cord should be covered with a minimum of 200 mm of sand or fine drill chippings.
- Cross-slips tend to terminate the developing split and spoil the end effect. Parallel slips act as points of least resistance, to which the excavation tends to break regardless of the pre-split.
- A coupling ratio of about 25% or less should be aimed for.
The following general considerations for trim blasting near pre-splits (Tose, 2006):
- Single-hole firing, particularly back rows
- Relatively long delays between rows
- Favourable relief (wide V)
- Longer stemming columns in back-row blastholes
According to the Explosives Engineers’ Guideline by Dyno Nobel (2025) the following general industry rules of thumb apply to pre-split blasting practices for surface mines:
- Hole spacing: 12x hole diameters.
- Burden: 0.5 x Production Burden.
- Uncharged length at the top of the hole: 10 x hole diameters.
- Powder Factor (PF): 0.5kg/m2.
- Stemming: Holes should not be stemmed.
- Timing: Fire all holes at the same time or in groups equal to or greater than 5 holes.
According to Dyno Nobel (2025) the powder factors typically relating to pre-split blasting vary according to the rock type blasted. Table 1 indicates the typical PF ranges relative to rock type.
Table 1. Typical Powder Factors for Pre-Splitting (Dyno Nobel, 2025)
Rock Type | PF (kg/m2) |
Hard Rock | 0.60 – 0.90 |
Medium Rock | 0.40 – 0.50 |
Soft Rock | 0.20 – 0.30 |
In the annual Programme in Blasting Engineering de Graaf (2021) noted the following key considerations for pre-split blasting:
- Radius of curvature >30 hole diameters – guide holes needed
- Quality is affected by hole spacing, charge mass per hole, charge mass distribution in holes (spacing is the most critical)
- No Free Face: Spacing = 6-10 hole diameters
- Free Face at some distance: Spacing = 8-12 hole diameters
- Free Face close to split: Spacing = 15-20 hole diameters
- Presplit holes should employ the smallest possible and particle size considering deflection, deviation, equipment available and number of holes to drill.
- Brittle Rock (Low Density): P=0.2-0.4kg/m2.
- Hard Rock (High Density): P=0.3-0.6kg/m2.
- Competent Sedimentary Rock: P=0.4-0.7kg/m2.
- Ideal decoupling ranges for presplitting is between 25%-33% (25% or lower in water prone holes).
- Stand-off to buffer holes must be at least 10 hole diameters.
- Wet holes to receive reduced charge (25%-50% reduction depending on amount of water).
- Presplit holes should be fired instantaneously when possible (In sensitive areas fire in batches of 5 or 10 depending on sensitivity level).
- Ensure, where possible, presplit planes do not undercut major joint systems
- Ensure GOOD DRILLING CONTROLS.
The relationship between mass of explosives per metre in the hole, hole spacing and split factor is defined by de Graaf (2021) as follows:
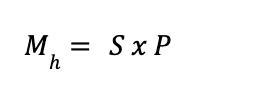
(Eq.1)
Where;
Mh = Mass of Explosives per metre in the hole (kg/m)
S = Hole Spacing (m)
P = Split Factor (kg/m2)
Konya (2019) conducted his PhD research on the topic: “The Mechanics of Precision Presplitting” and it is a good source of literature for anyone seeking to go into more depth regarding the theory behind pre-split blasting. An exhaustive discussion is not included in this article and the reader is directed to the original source should more information be desired. Konya challenged the prevailing shockwave theory as he believes there is a lack of comprehensive mechanistic models that accurately predict the formation of pre-splits across various geological conditions. His research aimed at developing a new model that is based on hoop stress caused by gas pressure from the decoupled explosive charges within the boreholes. The methodology followed included; empirical analysis of field data from various rock types to relate borehole pressures to explosive loads, theoretical modelling using a thermodynamic model to compute the borehole pressure and finally using mechanical models for hoop stress and shockwave analysis to investigate stress generated relative to the required tensile strength of the rock blasted.
In his research, Konya (2019) gives the following guidelines for pre-split designs:
- Explosive column loads should be designed based on the tensile strength of the rock, not traditional empirical rules.
- Apply the Konya Presplit Factor (K) as a design parameter to relate rock strength to explosive load and spacing.
- Borehole spacing must be adjusted to ensure overlapping hoop stress fields.
- Use decoupled charges in small-diameter holes with controlled gas pressure buildup.
- Adjust designs for specific geological conditions: weak rocks, jointed zones, or bedding planes.
- Avoid overloading charges to prevent overbreak and gas infiltration along natural planes.
Based on the first-hand site experience of ERG Industrial employees (in particular Mr. Louis van Heerden with 20+ years’ experience), the guidelines in Table 2 have been derived. There exists an opportunity to employ the rock mass properties, such as UCS and/or drilling penetration rates to practically adjust the splitting factor for the given are to be blasted. This allows for more precise optimisation of the design according to geological conditions observed.
Table 2. Guidelines based on site experience
Rock Type |
Drilling Penetration Rate |
Split Factor |
Soft Rock |
>40m/h |
0.1-0.3 kg/m2 |
Medium Rock |
25-40m/h |
0.3-0.5 kg/m2 |
Hard Rock |
<25m/h |
0.5-0.9 kg/m2 |
According to Hoek (2023) where possible, undamaged faces should be used to estimate the value of Geological Strength Index (GSI), indicated in Figure 2, towards determining the properties of undisturbed rock masses.
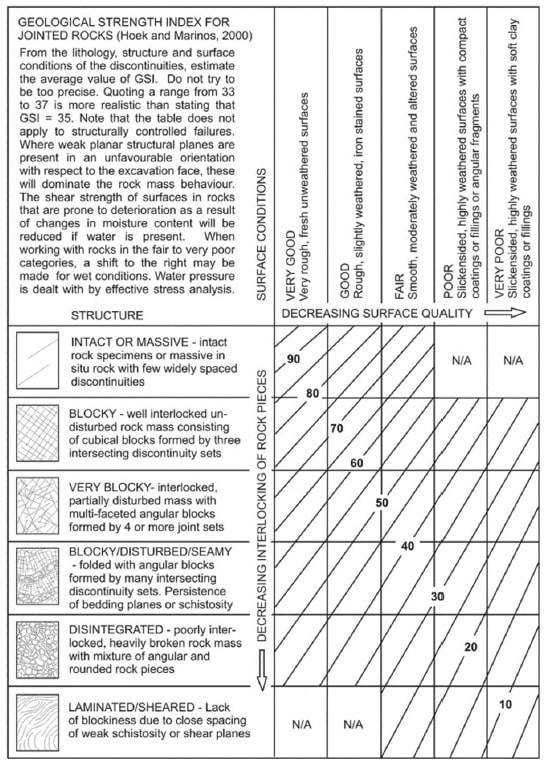
Figure 2. GSI matrix: Characterisation of blocky rock masses based on interlocking and joint conditions (Hoek, 2023)
There exists a practical problem when assessing GSI relating to blast damage, as evident in the considerable difference in the rock face appearance post excavation in areas of controlled blasting versus bulk blasting (Figure 3).
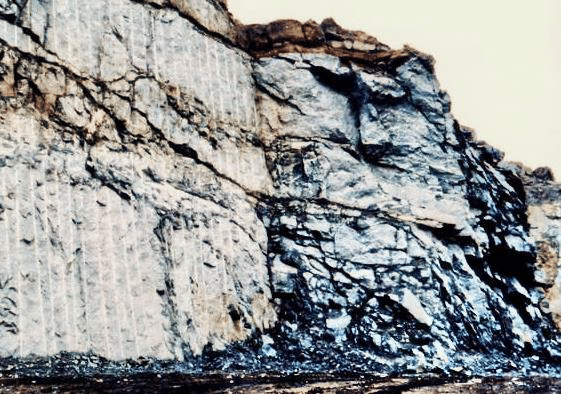
Figure 3. Comparison between the results achieved using controlled blasting (on the left) and normal bulk blasting for a surface excavation in gneiss (Hoek, 2023)
Regardless of the rule of thumb followed, the drill and blast engineer should ensure a systematic approach is employed. The recommended methodology is as follows:
- Establish site specific conditions (geotechnical, geological, in-pit conditions and any associated challenges).
- Identify current practices and establish a baseline performance of current blasting outcomes (planned vs actual).
- Review current practices for alignment to industry rules of thumb.
- When re-designing or designing for the first time, use site specific context and then assign values to key parameters based on available rule of thumb ranges. If there is uncertainty or absence of key information, always start in the middle of the range and adjust the parameter up or down according to results observed.
- Continuously monitor planned vs actual conformance and post-blast results.
- Use all available information to incrementally adjust key parameters until desired outcomes are met.
Pre-Split Blasting Audit and Continuous Optimization Methodology
Wall control performance should ideally be reviewed on a continuous basis to validate geotechnical performance and operational success. When auditing pre-split blasts, the following auditing components are key:
- Monitoring drilling deviation and alignment
- Verifying powder factor and stemming depth compliance
- Evaluating slope profiles against design
- Analyzing blast vibration and flyrock control
In order to appropriately qualify design decisions, establishing context relating to geological, geotechnical and blast design parameters is critical. To further delineate the context a timeline for the operation should be established which will assist in identifying the required design requirements for the specific timeframe evaluated (see Figure 4).
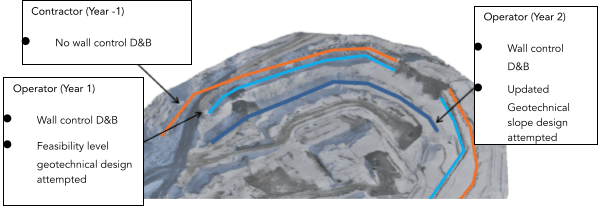
Figure 4. Timeline establishment for geotech- and drill & blast design requirements (After Sanders & Tims, 2025)
According to Saunders and Tims (2025), the evaluation process involves establishing geological and operational context, deploying performance monitoring tools, and implementing a structured design decision roadmap (see Figure 5).
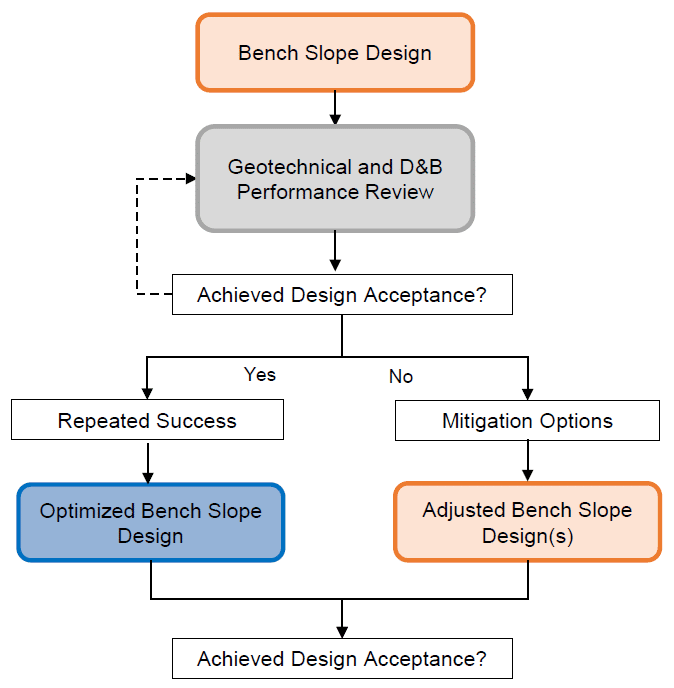
Figure 5. Final wall design decision roadmap (Sanders & Tims, 2025)
Regular pre- and post-blast inspections, digital as-built surveys, and use of accelerometer data help optimize designs. Repetition, stakeholder collaboration, and early performance reviews are essential for effective wall control. Table 3 is an example of how the relevant design decisions for final wall control is related to geological-, geotechnical- and drill and blast performance context.
Table 3. Establishing context for appropriate design decisions (Sanders & Tims, 2025)
Geological Considerations |
Drill and Blast Performance |
Geotechnical Performance |
Design Decisions |
Well understood |
Reasonable |
Anticipated |
Geotechnical design suitable and can identify opportunities |
Well understood |
Reasonable |
Poor |
Geotechnical design unsuitable |
Well understood |
Poor |
Poor |
Opportunity to improve |
Not well understood |
Poor |
Poor |
Significant efforts required to understand all components |
The following diagrams (Figure 6, Figure 7) depict a proposed iterative process to follow for trim- and pre-split blasting optimization respectively.
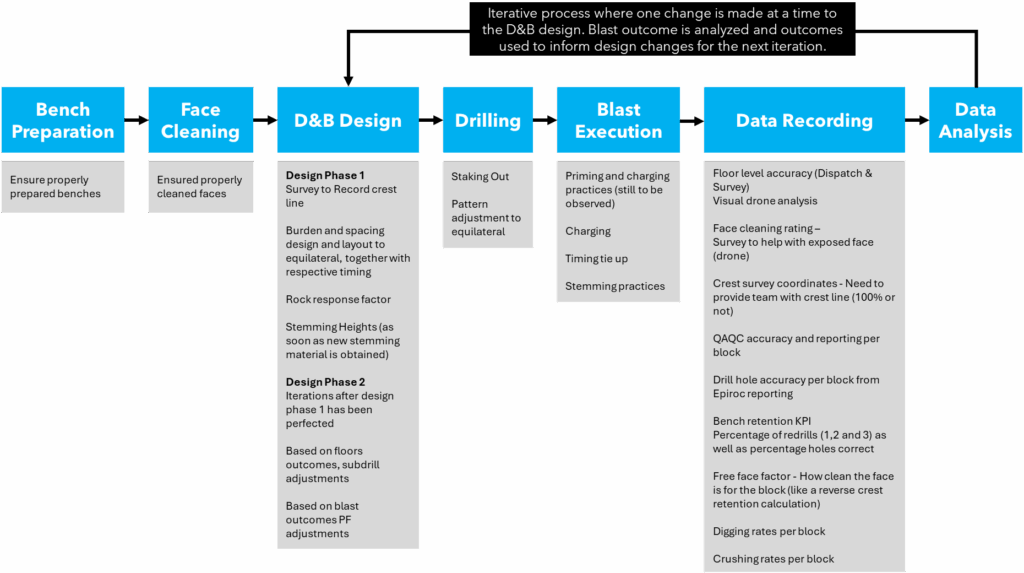
Figure 6. Iterative Trim Blasting optimization process
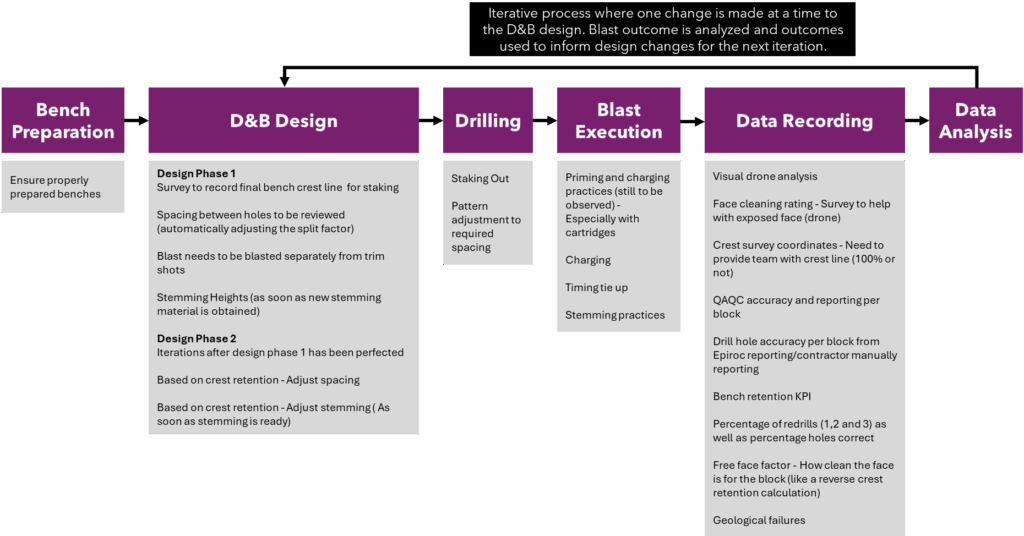
Figure 7. Iterative Pre-split Blasting optimization process
4. The Risks of Not Doing or Optimizing Pre-split Blasting
Neglecting pre-split blasting or implementing it poorly can result in technical-, safety-, and financial issues. Although not an exhaustive list, mines, quarries, or civil works can encounter the following risks when avoiding pre-splitting or due to poor execution of pre-splitting:
- Highwall Instability: Overbreak and uncontrolled cracking compromise slope integrity.
- Ground Control Costs: Poor walls require bolting, screening, or shotcrete to stabilize.
- Ore Recovery Losses: Damage to ore boundaries can lead to dilution or loss of recoverable material.
- Safety Hazards: Increased risk of flyrock, slope failures, and injuries.
- Economic Consequences: Increased stripping ratios, equipment needs and reduced Life of Mine.
Real-world examples show that mines implementing consistent pre-split programs avoid costly remediation and achieve better operational sustainability. Conversely, lack of pre-split programs often results in irreversible wall damage and production disruptions. Due to the arduous nature of pre-split programs, it is recommended that an iterative approach be followed to establish the best recipe for success and to obtain assistance from an expert consultant should the standard rules of thumb not yield the desired outcomes.
5. Conclusion
The purpose of pre-split blasting in mines and quarries typically includes; achieving safe highwalls for the safety of people and equipment working around highwalls, to maintain the integrity of final highwalls, benches, safety berms, and overall pit slope angle for life of mine, for dewatering of active blast blocks in advance, to reduce ground vibrations from adjacent production shots, to maintain consistent front row burdens, to provide a stable base for waste dumps, to eliminate crest backbreak and finally to protect critical temporary infrastructure zones (major haul roads, in-pit crushers, electrical substations, etc.). In civil industries, pre-splitting is commonly used in the construction of highways, tunnels, dams, and slope stabilization projects with the objective to produce clean and stable cut slopes that minimize long-term maintenance and reduce the risk of rockfalls.
Pre-split blasting remains one of the most effective and proven techniques for highwall control in mining, quarrying and construction. When properly executed, it ensures safer, more stable, and economically viable slopes. The method demands precision, dedicated QAQC, and adaptability. A structured audit and continuous improvement approach ensures that pre-split designs evolve with geological and operational contexts. Ignoring this process poses major risks to both safety and profitability.
References
Chiappetta, R., 2014. Presplitting and Highwall Controls: 12 Rules to Guarantee Results. Proceedings of IQPC Drill & Blast Africa, 20-21 October 2014. Johannesburg, South Africa, Blasting Analysis International Inc.
de Graaf, W., 2021. Surface Mining Explosives Application. In: Programme in Blasting Engineering, 19 February – 15 October 2021. Pretoria, University of Pretoria, Business Enterprises.
Dyno Nobel, 2025. Explosives Engineer’s Guide, s.l.: Dyno Nobel Asia Pacific Pty Limited.
Hoek, E., 2023. learning/hoeks-corner/5.-Rock-mass-properties. [Online]
Available at: https://static.rocscience.cloud/assets/resources/learning/hoek/5.-Rock-mass-properties_2023-06-30-120618_sdtd.pdf
[Accessed 11 July 2025].
Konya, A., 2019. PhD: The mechanics of precision presplitting, Missouri, USA: Missouri University of Science and Technology.
Sanders, E. & Tims, S., 2025. Qualifying the Wall Control Drill and Blast Influence on Geotechnical Bench Design. Proceedings of CIM Connect, 4-7 May 2025. Montreal, Canada, SRK Consulting.
Tose, S., 2006. A REVIEW OF THE DESIGN CRITERIA AND PRACTICAL ASPECTS OF DEVELOPING A SUCCESSFUL PRE-SPLIT. In: International Symposium on Stability of Rock Slopes in Open Pit Mining and Civil Engineering. Cape Town, The South African Institute of Mining and Metallurgy.