The purpose of the Varistem® stemming plug trial conducted at Coal Mine X was to reduce flyrock, noise, and airblast by retaining blast energy. The trial area is close to a neighboring farm within the 500m blast radius. By analyzing drilling and charging data for each hole, the Scaled Depth of Burial (SDoB) was determined to predict flyrock levels without using Varistem®. Despite an average SDoB indicating potential violent flyrock, the actual blast showed excellent energy retention, with flyrock reaching no more than 100m from the blast. Considering the difficult conditions (shallow holes and low stemming), the results suggest that Varistem® plugs effectively helped mitigate flyrock. The details pertaining t0 the blast set-up is indicated in the table below.
Number of holes | 218 |
Average drill depth | 2.08m [shortest hole = 0.4m] |
Average stemming height | 1.04m |
Hole diameter | 171mm |
Average SDoB | 0.53 |
Table 1. Blast Setup: Flyrock Study
According to the scaled depth of burial measurements, it was anticipated that many holes in this trial blast will generate intense flyrock. Please note that these SDoB values were derived from actual charging and drilling data.

WHAT IS FLYROCK?
Flyrock refers to fragments of rock propelled from the blast site beyond the designated clearance zone, posing potential dangers to personnel, equipment, and nearby structures (Esen, 2016). The clearance zone is the designated area around the blast site from which all personnel and equipment must be evacuated before the blast (Stiehr, 2011).
Flyrock happens when the explosive force of a blast exceeds the rock mass’s ability to contain it. This can occur due to various factors, such as inadequate blast design, incorrect loading or stemming, excessive explosive charges, or unfavorable geotechnical conditions leading to insufficient confinement of the blast energy. The size, velocity, and trajectory of flyrock fragments can vary greatly, ranging from small particles to large boulders that can travel considerable distances from the blast site. The primary mechanisms of flyrock generation, as illustrated in Figure 1, are categorized into Face Bursting, Cratering, and Rifling.
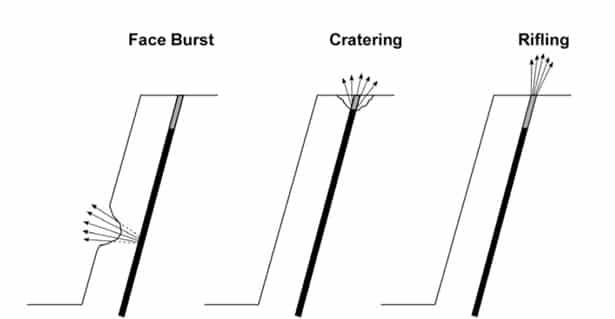
For more in-depth details regarding this concept, please view our technical article on minimizing the risk of flyrock in mine and quarry blasting.
WHAT ARE THE DANGERS OF FLYROCK?
- Injury or Fatality: Flyrock poses a direct physical hazard to workers, bystanders, and nearby structures. If a person or property is hit by flyrock, it can result in serious injury or even death.
- Property Damage: Flyrock can cause damage to nearby structures, vehicles, and equipment, leading to costly repairs or replacements.
- Environmental Damage: Flyrock can disturb the surrounding environment, including vegetation, wildlife habitats, and water bodies, leading to ecological disruption and potential contamination.
- Legal and Regulatory Consequences: Accidents involving flyrock can result in legal liabilities, fines, and regulatory penalties for the responsible parties, as they may be found in violation of safety regulations and environmental laws.
- Public Perception: Incidents involving flyrock can damage the reputation of the companies involved and erode public trust in the safety of blasting operations, leading to negative publicity and potential loss of business opportunities.
HOW DO YOU MITIGATE FLYROCK?
To mitigate the risks associated with flyrock in blasting activities, crucial measures such as optimizing blast design, establishing clearance zones, complying with regulations, monitoring and controlling blasts, providing personnel training, raising public awareness, and enhancing communication are essential. Effective blast design involves considering factors like geology and rock properties, optimizing blast parameters, and using tools like the Scaled Depth of Burial (SDoB) principle and Varistem Stemming Plugs to ensure proper energy containment. Exclusion zones should be marked to prevent unauthorized access, and adherence to laws and regulations, such as those outlined by the Department of Mineral Resources and Energy in South Africa, is necessary. Blast monitoring systems aid in real-time feedback and control, while comprehensive personnel training ensures safe practices. Public awareness efforts, including communication with nearby communities, further contribute to flyrock mitigation by fostering understanding and cooperation.
FLYROCK CASE STUDY DATA
The following images are screenshots taken from the footage of the blast conducted for the Flyrock case study. These images depict the analysis of the flyrock from a visual perspective.
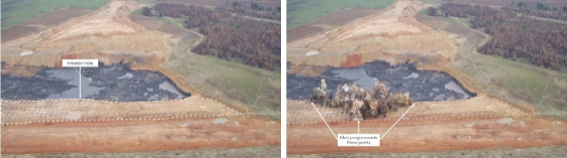
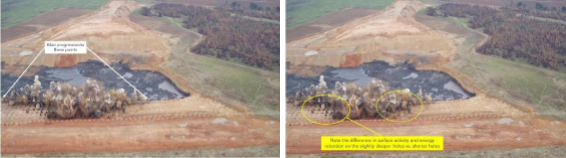
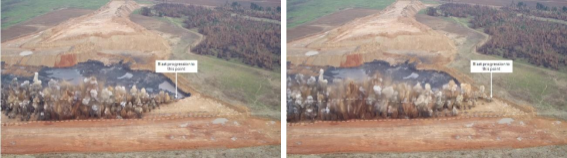
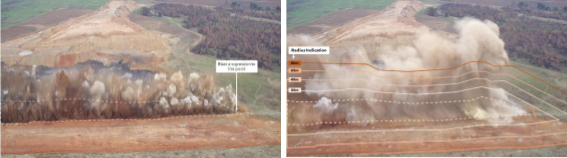
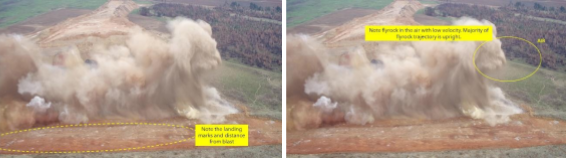
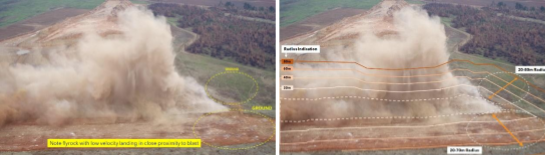
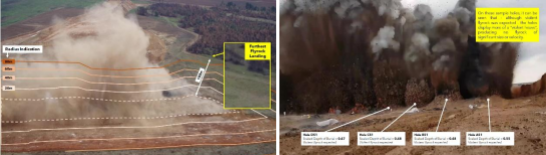
FLYROCK CASE STUDY FINDINGS
Considering the calculated SDoB values and the associated theory, it was expected that the majority of holes in the trial block would produce violent flyrock. However, upon reviewing the footage, it is evident that contrary to this expectation, there were relatively low levels of flyrock across the entire block, with the furthest flyrock estimated to have travelled approximately 100m away from the block. Upon closer examination of the block footage and the blast propagation mechanism for individual holes, it becomes apparent that the holes exhibited more of a “violent heave” rather than violent flyrock, with no flyrock of significant size or velocity visible. Based on the above observations, it can be inferred that the utilization of Varistem® plugs contributed to the mitigation of flyrock and effectively increased the SDoB values by containing more energy within the rock mass. However, it is important to note that more conclusive findings could be drawn by comparing this trial blast result to a block with similar characteristics but not using Varistem®.
FLYROCK CASE STUDY CONCLUSION
ERG Industrial is highly satisfied with the trial outcome and believe that the Varistem®’s capabilities regarding flyrock mitigation was clearly demonstrated in the results from this case study. If you would like to find out more regarding this concept, please contact us and we’ll put you into contact with the relevant expertise.